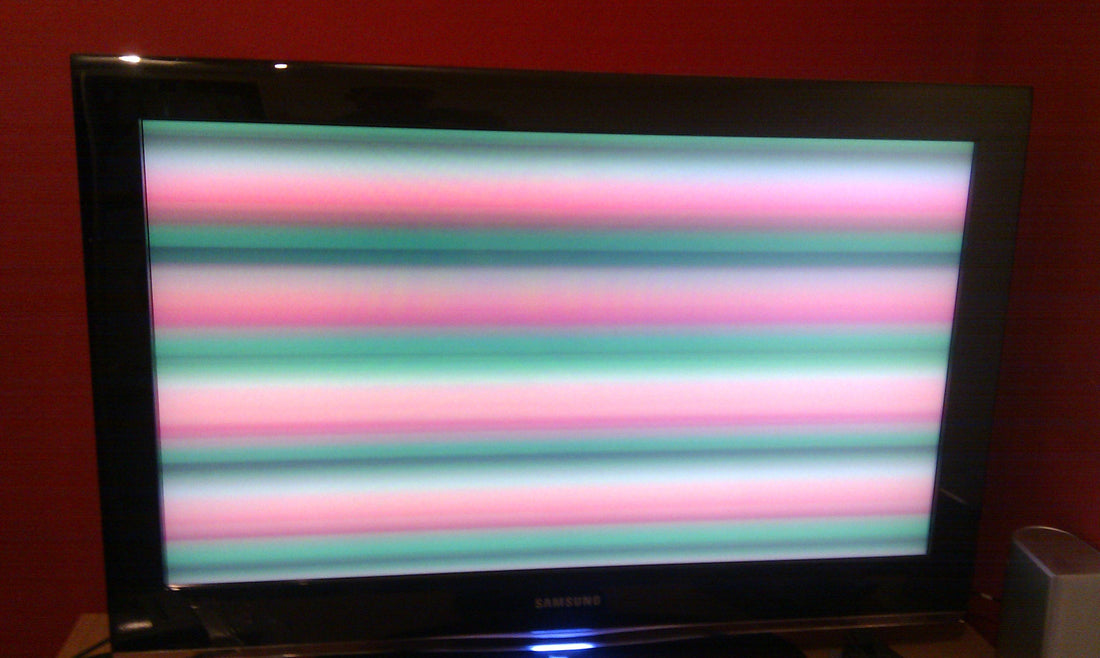
DEAD PIXELS RUINING MY SCREEN - THIS NEVER HAPPENED IN THE OLD DAYS! (ii)
Share
Today, let's look at the process for tube screen (or faceplate) manufacture that was employed by Mullard in the early 1950s. If we had visited Mullard's tube manufacturing area we would have seen a tank holding 250 tons of molten glass and nearby, a work bench holding moulds which were contoured to match the required screen shape. Glass blowers working in this area armed with iron rods, topped with a ball of fire clay would dip their implement into the molten glass tank and withdraw a bolus of molten glass known as a 'gather'. The 'gather' would be held over a mould and with a quick jiggle, gravity would cause the treacly molten glass to flow into the mould. The molten glass would spread slowly within the confines of the mould with final shaping being helped along by a power operated plunger that would descend to press the glass to fill the mould hence completing the faceplate.
I am sure that having read the account above, two things may be appreciated, first, how manual and potentially dangerous the manufacturing process was and secondly, the potential for marking of faceplates was pretty great. As can be appreciated, when the 'gather' first strikes the relatively cold mould, it starts to solidify, causing an arc shaped mark in the centre of the faceplate. These marks were termed gather marks and were usually seen on the outside surface of a faceplate and looked a little like this: -
As the 'gather' broke away from the transfer rod and plopped into the mould, again, a surface blemish could occur, again in the form of an arc but this time pointing toward the faceplate centre. These marks termed shear marks were usually found on the inner surface of the faceplate and looked a little like this: -
Where localised cooling occurred when the initial flow of glass over the mould resulted, sometimes the central portion of the faceplate could have a polished appearance whilst the remainder was noticeably matt. In order to reduce this defect, every mould would be reground daily or even chromium plated to reduce the occurence of this blemish known as matt & polish which looked a little like this: -
The above described examples comprised the most commonly seen and hence troubling faceplate or screen blemishes, however, there were more...... If the face of a 1950s moulded tube were examined closely, four small glass pips could be seen around the peripheral endge of the faceplate surface - these artefacts correspond to vent holes which were provided in the plunger to permit the escape of air trapped betwixt plunger and mould. The pips were carefully placed to be in the extreme corners of the faceplate when the tube was installed in a TV receiver.
When you consider that faceplates were produced by a manual process in an industrial environment, occasionally tiny ripple marks, very small bubbles and foreign matter such as sand or scale particles could end up embedded in the faceplate as well.
Next time, we'll disuss the quality control checks that Mullard applied to minimise detection of these blemishes by a discerning consumer populace.