THE GREAT MULLARD MAGIC BLOG
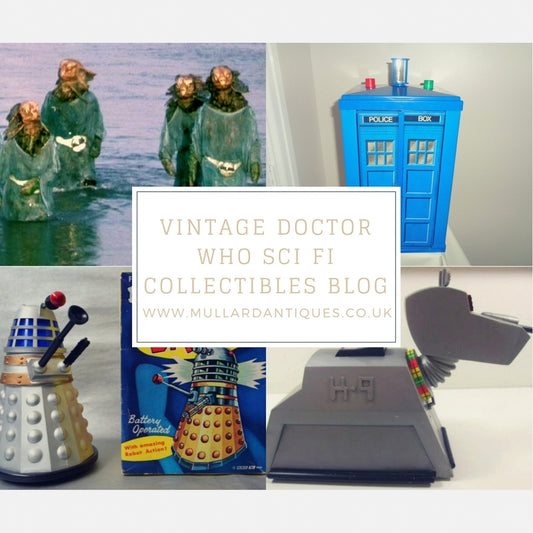
Vintage Doctor Who Sci Fi Collectibles
This is the fifth in a series of guest blog posts that I will be sharing with my readers. A small group of us, all with different backgrounds and geographical locations, have...
Vintage Doctor Who Sci Fi Collectibles
This is the fifth in a series of guest blog posts that I will be sharing with my readers. A small group of us, all with different backgrounds and geographical locations, have...
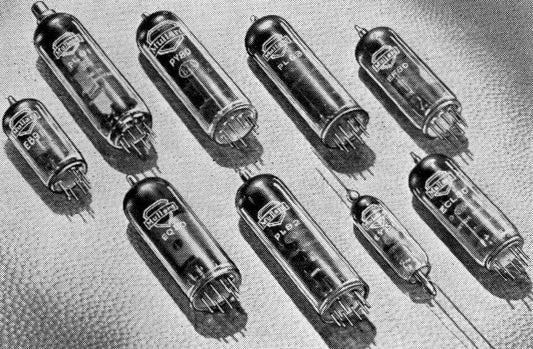
THE MULLARD WORLD SERIES OF TELEVISION VALVES
The advances in television since WW2 and the extension of the British TV service and indeed those of other countries brought with it the necessity to develop a more effective...
THE MULLARD WORLD SERIES OF TELEVISION VALVES
The advances in television since WW2 and the extension of the British TV service and indeed those of other countries brought with it the necessity to develop a more effective...

OOJAH, PILES AND RADIOS
How we smiled when we saw this 1924 advert for a Graphite Pile Rheostat. With it's connotations of 'pile' and near onomatopoeic sound of Oooyah, a classic expression of pain,...
OOJAH, PILES AND RADIOS
How we smiled when we saw this 1924 advert for a Graphite Pile Rheostat. With it's connotations of 'pile' and near onomatopoeic sound of Oooyah, a classic expression of pain,...

TUBES TURN UP IN STAR TREK TOS ONCE AGAIN!
We recently left our two part Star Trek blog wondering whether or not thermionic technology ever again appeared in episodes moving on from the pilot episode, The Cage and the...
TUBES TURN UP IN STAR TREK TOS ONCE AGAIN!
We recently left our two part Star Trek blog wondering whether or not thermionic technology ever again appeared in episodes moving on from the pilot episode, The Cage and the...

CAN YOU TELL ME ABOUT MULLARD TROPICAL FISH CAP...
Again, I shall pause from my historical Mullard meanderings to answer a query I have received from a customer from Malaysia about the Mullard ‘Tropical Fish’ capacitors, so called due...
CAN YOU TELL ME ABOUT MULLARD TROPICAL FISH CAP...
Again, I shall pause from my historical Mullard meanderings to answer a query I have received from a customer from Malaysia about the Mullard ‘Tropical Fish’ capacitors, so called due...
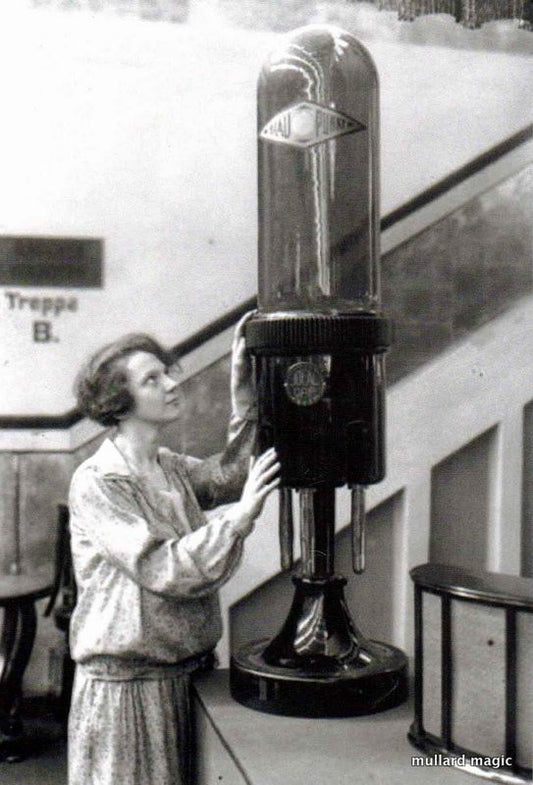
OOOH! GIRLS LIKE BIG UNS A LOT!
Well, whatever did you think, shame on you......... You know, it is said that there is nothing new in show business or advertising and here we have three photos just...
OOOH! GIRLS LIKE BIG UNS A LOT!
Well, whatever did you think, shame on you......... You know, it is said that there is nothing new in show business or advertising and here we have three photos just...